Electro-hydraulic Load Cells for Steel Linings and Struts

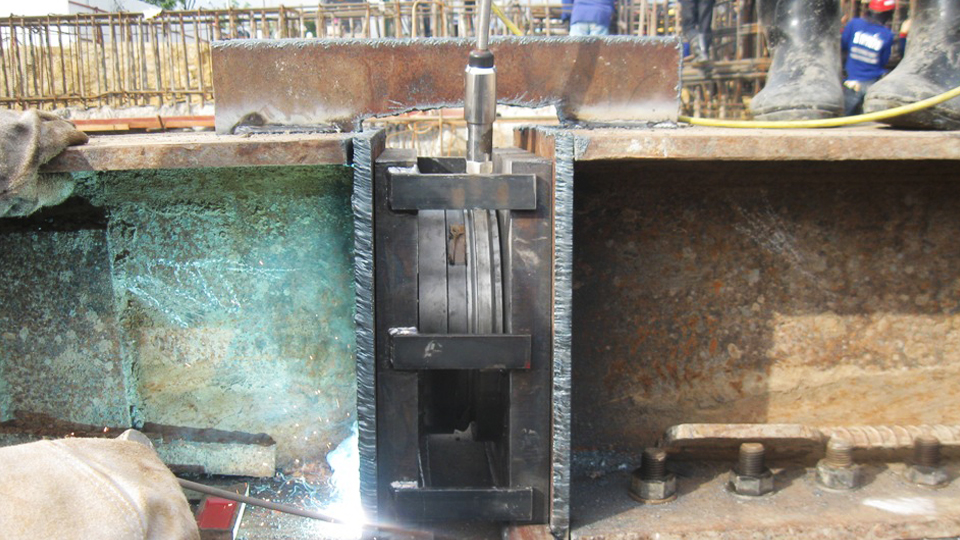
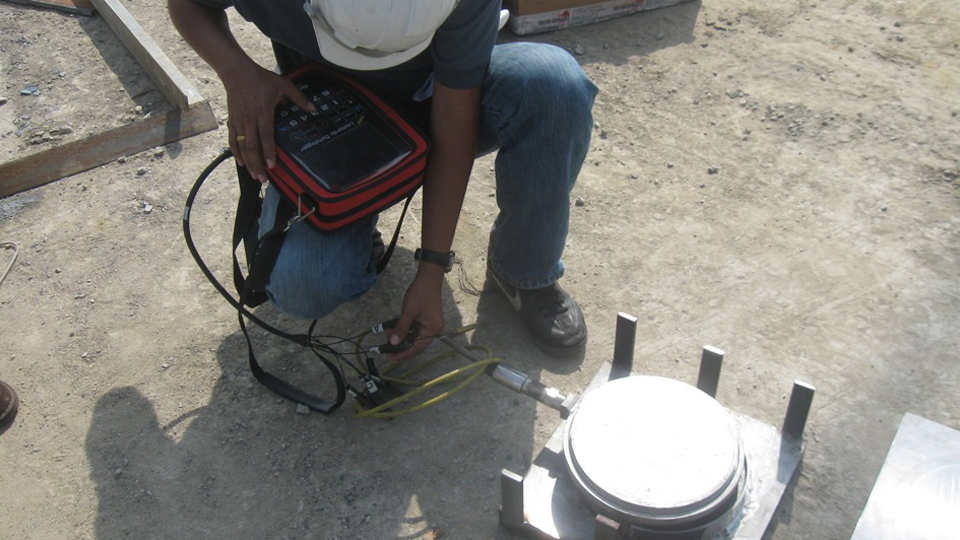
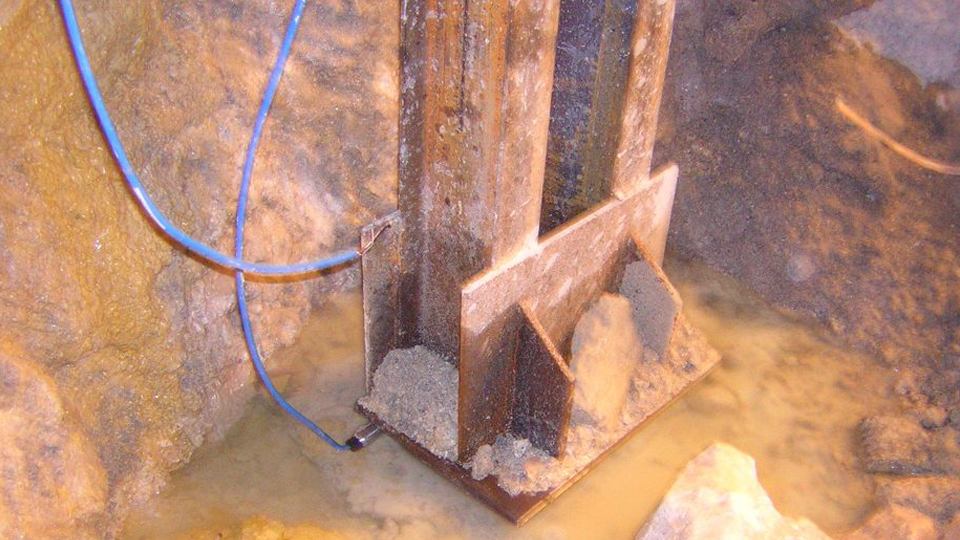
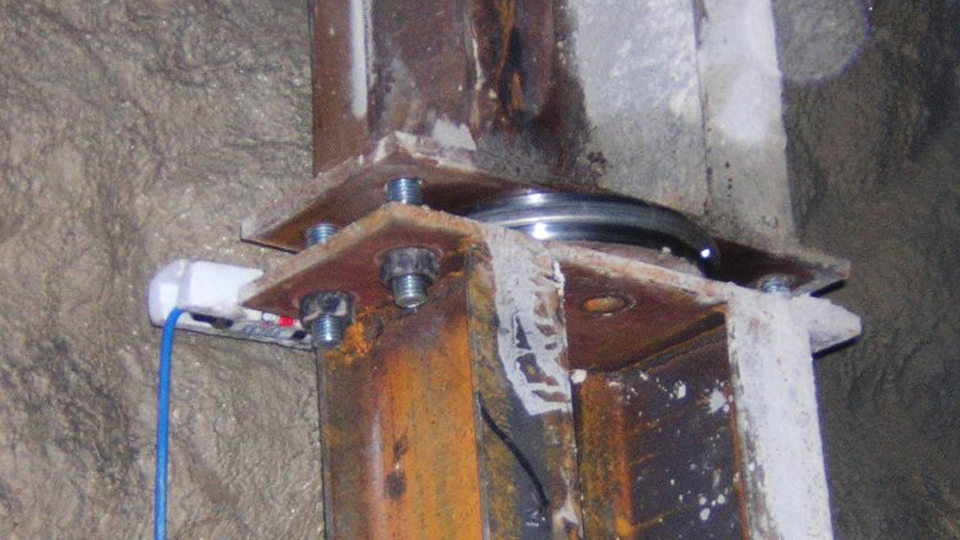

Electro-hydraulic load cells consist of stainless steel pad with a pressure transducer.
The piston pad is realised by two plates welded together around their periphery and spaced apart by a narrow cavity saturated under high vacuum with de-aired oil to assure maximum rigidity; so that load is transmitted into a pressure measured by the pressure transducer.
They are specially designed for steel lining and struts monitoring.
Special twin distribution plates are available for application between not parallel surfaces.
Resistive pressure transducer sensor is a spin off from thick film technology using the piezo-resistive characteristic of specific resistive inks. Resistors, formed using screen printing techniques, are deposited on a deformable ceramic diaphragm substrate to form strain gauge arrays. Strain changes from external loads applied to the deformable ceramic diaphragm result in resistance changes of the strain gauge arrays.
The electric signal from the strain gauge arrays is directly proportional to the stress applied to the diaphragm. Sensor is constructed of a ceramic, analogous to a crystal structure, to form a pressure diaphragm chemically inert with near perfect mechanical characteristics. Screen printed resistors are deposited onto the diaphragm to form a 4 arms Wheatstone bridge.
A fixed excitation voltage is applied to one diagonal of the circuit. Strains experienced by the diaphragm will change the values of the individual resistors within the Wheatstone bridge resulting in a bridge unbalance. This unbalance produce an output signal from the other diagonal of the Wheatstone bridge, directly proportional to the applied stress.
An electronic board converts this signal into 4-20 mA suitable for transmission over long distances to remote readouts or to data acquisition systems.
Readable by
Questions
about this
product?
about this
product?
Questions
about this
product?
about this
product?
Datasheet
Manual
Data processing
Faq