Solid Resistive Load Cells for Pile Testing
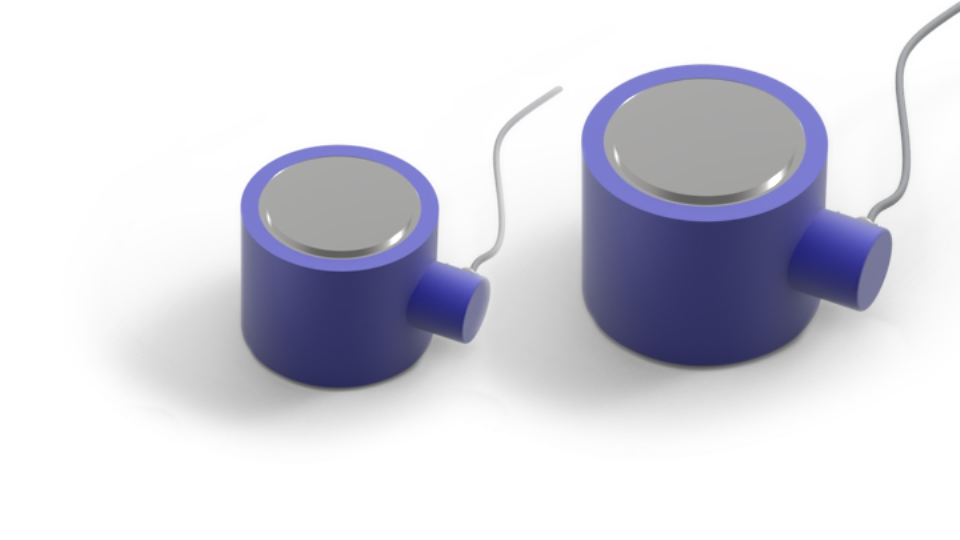
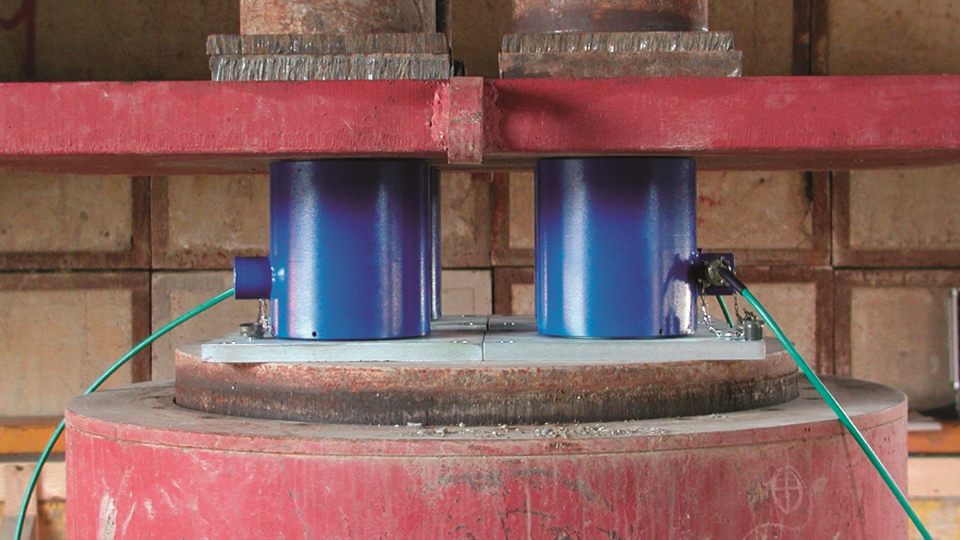
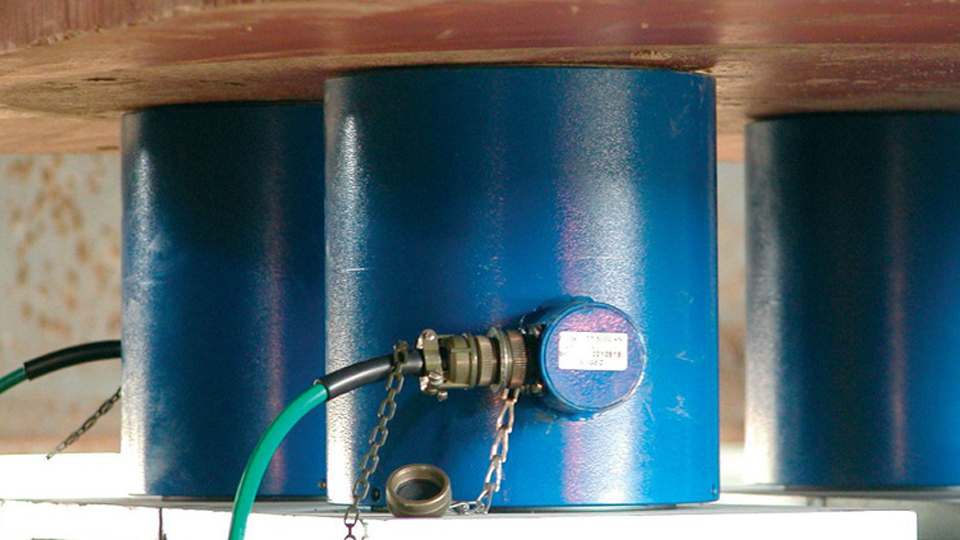
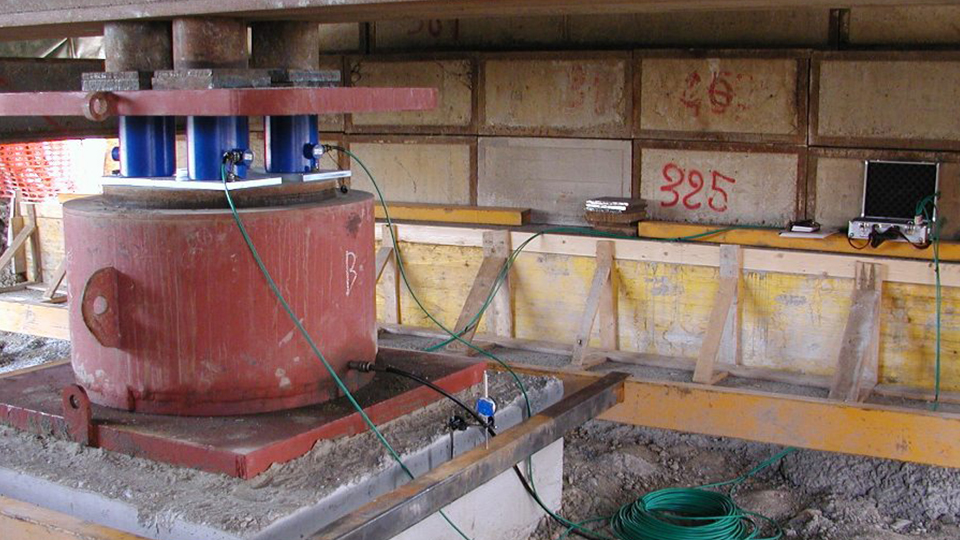
Specially designed for pile testing, they consists of a cylinder body made by heat-treated steel instrumented with 4 strain-gauges.
Customised range available to suite any request.
L2CT load cells are tested for long-term stability under heavy operating conditions.
Electric cable can connect load cells to a suitable remote datalogging system for real time monitoring.
Any common piece of wire will change resistance slightly when placed under tension. Wire arranged to maximize this effect forms a strain gauge. Strain gauges are typically etched foil patterns glued to a bar of metal or other tensionable material.
In a load cell, strain gauges are placed so that when the cell is loaded, the gauges are strained, changing their resistance. The resistance change per unit of strain is very small. To measure such small changes in resistance or voltage, these sensors are almost always used in a bridge configuration with a voltage excitation source. The general Wheatstone bridge consists of four resistive arms with an excitation voltage that is applied across the bridge.
Different configurations existing:
• single-point bridge sensor (a single resistor changes, while the other three are fixed)
• two-point bridge sensor
• four-point bridge sensor (all four elements varying).
The last one, also name “full bridge configuration” is the bridge type used in SISGEO instruments because very linear and sensitive output is needed.
When the instrument is connect with a long cable (>50mt) it is necessary to reduce errors arising from voltage drops in the excitation line, so 6 wires are necessary to be wired to the readout/datalogger using 2 analog inputs, one to measure the output voltage and the other to measure the excitation voltage. The voltage drop is then divided by the excitation voltage to find the ratio between the two.
Readable by
Questions
about this
product?
about this
product?
Questions
about this
product?
about this
product?
Datasheet
Manual
Data processing
Faq